My current research focus is modeling friction and wear in material forming, multi-scale material modeling and optimization of manufacturing processes related to material deformation. My research activities are supported by key Dutch and European industrial partners mainly in steel, aluminum and automotive sectors. My educational activities are mainly in Mechanical Engineering and Industrial Design programs at different levels: BSc. (Finite Elements Method; Design and Mechanics), MSc. (Computational Structural Optimization) and PhD. (Mechanics of Large Deformations; Nonlinear Material Mechanics).
Organisations
My current research interests are:
- Modeling friction and wear in material forming
- Multi-scale material modeling
- Modeling manufacturing processes related to material deformation
- Surface engineering and texture design in sheet metal forming
Publications
Jump to: 2024 | 2023 | 2022 | 2021 | 2020
2024
2023
2022
2021
2020
Research profiles
Affiliated study programs
Courses academic year 2025/2026
Courses in the current academic year are added at the moment they are finalised in the Osiris system. Therefore it is possible that the list is not yet complete for the whole academic year.
Courses academic year 2024/2025
Courses academic year 2023/2024
- 191199152 - Internship
- 195799152 - Internship
- 201300176 - CS1 EngD Robotics
- 201300295 - Professional Development - EngD
- 201300298 - Literature Study - EngD
- 202000149 - Intro. Finite Element Method
- 202000214 - Introduction to Finite Element Method
- 202000250 - Internship
- 202001537 - Applied Mechanics - Capita Selecta
- 202200127 - Computational Optimization
- 202300353 - Internship (CSE/SET)
Below is the list of projects funded by Netherlands Organization for Scientific Research, EU and industry.
Current projects
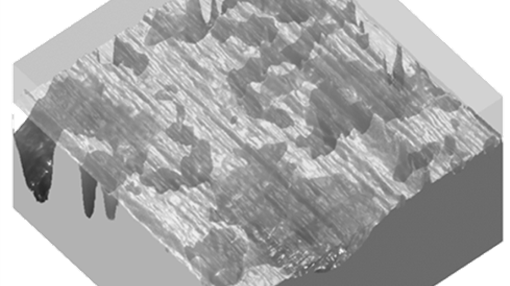
A micro-mechanical model for roughness transfer in cold rolling of steel strips
Emerging of the “smart” industry 4.0 technologies challenges the conventional manufacturing processes such as rolling of the steel strips. In this regard, automotive and packaging industries requirements on surface texture of the steel strips are becoming increasingly stringent. Surface texture determines the visual appearance and tribological behavior of the strips. The goal of this project is to understand the fundamental physics of the roughness transfer from a textured roll surface to a metal strip surface and to develop a physical roughness transfer model that predicts the final surface properties of the strip based on the rolling process parameters.
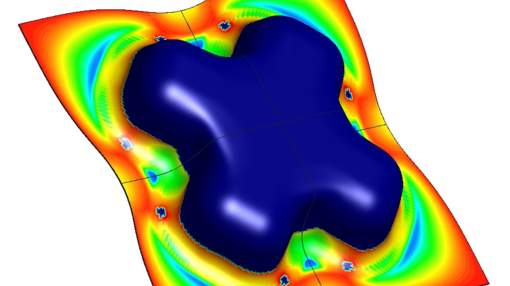
Multi-scale Friction Modeling in Aluminum Sheet Forming
FORMALUB
Friction is one of the key parameters in sheet metal forming processes which can directly affect the formability of the product. In a typical forming process, the coefficient of friction is a transient parameter and varies from location to location throughout the part due to evolution of the contact conditions at the tool-sheet metal interface. The contact condition in turn is a function of the topography of the contacting surfaces, contact loads, material and lubricant behavior and temperature. Nowadays, finite element (FE) analysis is a standard tool to study the formability of sheet metals in forming processes. However, a constant coefficient of (Coulomb) friction is generally used in the FE simulations which does not account for the evolving contact condition due to the change in contact loads during the forming process. This leads to inaccurate and unreliable results. Therefore, accurate prediction of coefficient of friction is of utmost importance for the accuracy of the formability analyses and thus a zero-defect production. In this project, a multi-scale friction model is developed that accounts for the significant variables that can influence the coefficient of friction.
Digital Twin: dealing with uncertainties in manufacturing processes
Model (simulation)-based optimization is nowadays a common tool in designing manufacturing processes where optimal use of material and process capabilities are utilized. However, this strategy is subjected to different types of uncertainties. As these uncertainties are neglected, very often an optimal deterministic process design is found which is at the limits of the material, process capabilities and the accuracy of the models. The uncertainties in the model-based optimization strategies are related to the inherent variations in the process inputs such as material properties, geometry, process settings (machine dynamics, lubrication) or changing environmental conditions (temperature). The other source of uncertainty in these strategies originates from the inaccurate or unphysical assumptions in the (Multi-scale FE or surrogate) models. The main goal of the project is to find the best model updating strategy based on measured input and output data. Such strategy is able to realize different sources of uncertainties, update the necessary parameters and reduce the discrepencies between predicted results and the measured output data.
Finished projects
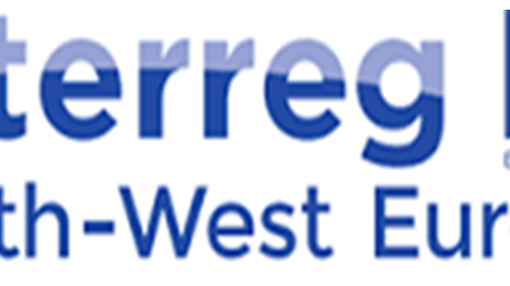
Advanced Simulation and control of tribology in metal forming processes
ASPECT
The ASPECT project, funded by the programme INTERREG North-West Europe, aims to create a reliable, robust framework to predict friction increase with temperature and to develop a control system that can instantaneously correct the applied forces to account for the sensed friction increase. For more information please visit ASPECT webpage at: www.nweurope.eu/aspect
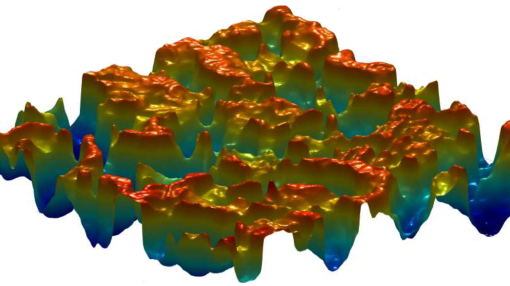
Model based surface texture design for zinc coated metal sheets
TXTURE-it
In sheet metal forming applications, friction is a determining process factor which typically varies from location to location and in time during forming. To pursue stable and desirable friction conditions, (zinc coated) sheet metal is nowadays surface finished with an isotropic texture, in combination with surface treatments and lubrication systems. However, a well-founded and optimized design of (multilayered) sheet surfaces with respect to their frictional behavior in sheet metal forming is not yet possible. The main aim of this project is model based surface design for multi-layered metal sheet based on fundamental physical insights to realize optimal frictional behavior in sheet forming processes.
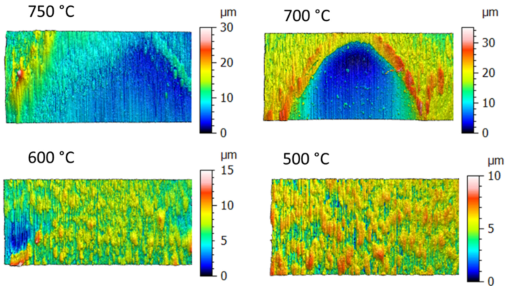
TRIBOLOGICAL INTERACTIONS AND MODELLING OF FRICTION IN HOT STAMPING
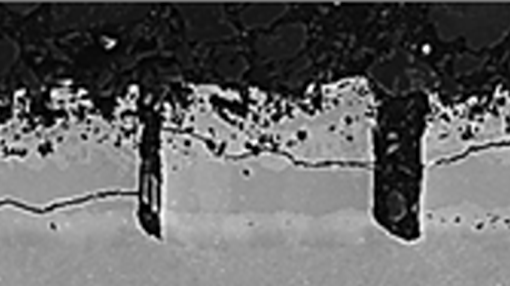
Characterization of Al-Si coating fracture during hot deformation
CRASCoat
Hot stamping is a widely used technology to produce ultra-high strength steel parts in the automotive industry. To avoid surface oxidation and decarburization at high temperatures, aluminum-based coated steel sheets are used. However, localized cracking and delamination of the Al-coatings are the major problems which can affect the determining process factors such as coating frictional behavior and tool wear. The aim of this project is first characterizing the initiation and cracking of the coating, second multi-scale modeling of the fracture behavior of the multi-layered Al-Si coating and third optimizing hot stamping process parameters to reduce coating fractures.
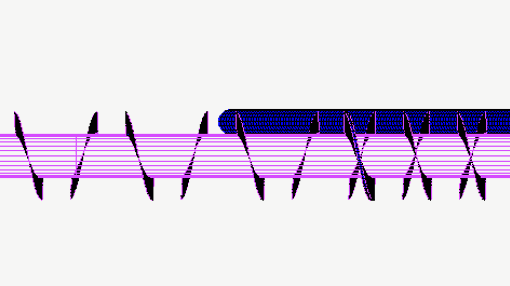
First time right production of metal conveyor belts by active control
Address
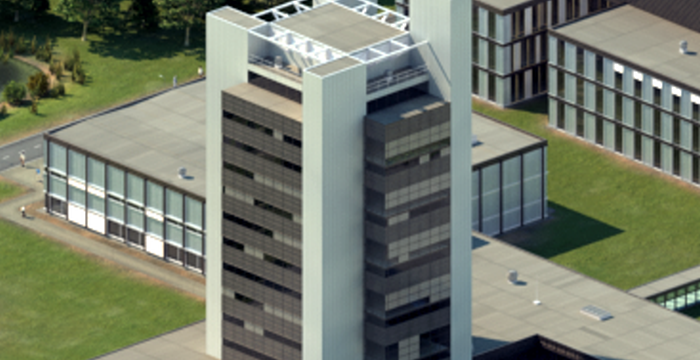
University of Twente
Horst Complex (building no. 20), room N146
De Horst 2
7522 LW Enschede
Netherlands
University of Twente
Horst Complex N146
P.O. Box 217
7500 AE Enschede
Netherlands