Jamal S. M. Zanjani is an assistant professor at the Surface Technology and Tribology (STT) group within the faculty of engineering technology. He holds a sectorplan position focusing on interface design for hybrid lightweight structures.
He obtained both his Bachelor's and Master's in Polymers Engineering and a PhD in Material science and Engineering with a research emphasis on the processing and mechanics of complex materials and composites.
He has received many awards and fellowships for his research activities, including the best thesis award for his PhD thesis, several presentation awards, Marie Skłodowska-Curie individual fellowship and several project grants.
His research focuses on creating correlations between processing, microstructure, properties, and product performance in multilateral hybrid structures. His group pays particular attention to the interphases and interfaces between the constituents as it is key to attain a reliable hybrid structure. His team develops experimental techniques as well as modelling tools to analyze and describe the physical mechanisms at the interface and exploit them for optimizing the short and long-term structural performances of hybrid structures.
His teaching activities cover different modules in mechanical engineering at undergraduate and graduate levels. He is also offering a graduate-level course on adhesion and bonding technologies.
Expertise
Material Science
- Composite Material
- Fiber
- Carbon Fiber
- Graphene
- Thermoplastics
- Temperature
- Polymer
- Glass
Organisations
Stationary contacts & bonding in hybrid structural materials
Hybridization of materials is defined as the process of combining two or more materials to optimally serve a specific purpose. Hybridization of materials is a potent strategy for creating material systems with properties that do not exist in a single material. Hybridization includes joining similar or dissimilar entities e.g. polymer-polymer, polymer-metal, polymer-ceramic, etc to obtain lightweight, yet reliable, predictable and robust load-carrying structural materials. Hybridization offers many advantages including:
- Right properties at the right place
- Weight reduction
- Improved performance
- Higher manufacturability
The performance of hybrid structural materials is largely controlled by the interfaces between their constituents. Therefore, we pay particular attention to the interphases and interfaces between the constituents. Our team develops experimental techniques as well as modelling tools facilitating the interface design for the next generation of advanced lightweight hybrid structural materials. It covers process design, surface pre-treatment, surface characterization, bond performance, and joint design. The group is well versatile in surface pre-treatment techniques and associated surface and interface characterization methods to analyse, describe and optimise the interface formation between various material pairs. The focus is on creating correlations between processing, microstructure, properties, and product performance at the interface to optimise the short and long-term structural performance of hybrid structures. We look for innovative engineering solutions through hybridization and new manufacturing techniques covering:
- Surface pre-treatment (Physical, mechanical, chemical)
- Surface/interface characterizations
- Adhesive bonding, co-bonding, polymer welding
- Additive manufacturing of thermoplastics
- Interface design for polymer-metal hybrids
- Thermoset-thermoplastic interphases
- Wind turbine production and maintenance
- Non-destructive testing/damage assessment
Publications
Jump to: 2025 | 2024 | 2023 | 2022 | 2021 | 2020
2025
2024
2023
2022
2021
2020
Research profiles
Affiliated study programs
Courses academic year 2024/2025
Courses in the current academic year are added at the moment they are finalised in the Osiris system. Therefore it is possible that the list is not yet complete for the whole academic year.
Courses academic year 2023/2024
- SectorPlan, Interface optimization for metal -thermoplastic hybrids
- Super fluent pipes – Pipes with ultralow fluid resistance
- Integrated leading edge protection for offshore wind turbine blades at high speed
Finished projects
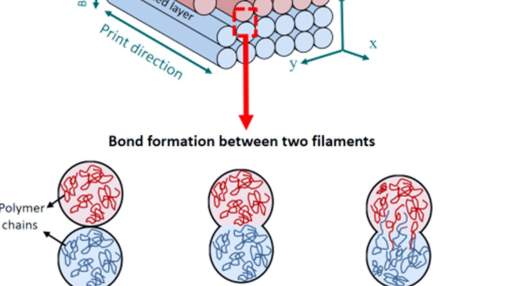
Additive manufacturing of thermoplastic composites
Marie Skłodowska-Curie Individual Fellowship (Print2fly)
With rising environmental concerns and fuel costs, we urgently need to reduce the weight of commercial aircraft to enhance fuel efficiency. Within the Print2fly project, the capabilities of additive manufacturing (AM) are combined with room temperature polymerization chemistry to fabricate thermoplastic composites with significant weight reduction and high recyclability. The adaption of aerospace-grade thermoplastics for conventional AM processes is extremely challenging, considering the complications associated with their high processing temperatures and melt viscosity. Within Print2fly an extrusion-based AM method named Reactive Liquid Deposition Modelling (RLDM) is developed to fabricate reliable and high-performance continuous fibre reinforced thermoplastic composites at room temperature. The RLDM technology replaces the conventional melt processing with photopolymerization of a liquid resin with tailored flow-ability and polymerization kinetics. The RLDM demonstrated promises to fabri-cate defect-free and first-time right parts by eliminating interface defects and voids. The RLDM technology extends the applicability of AM for printing large structures with customized design, reduced cost, and lower environmental impact.
Address
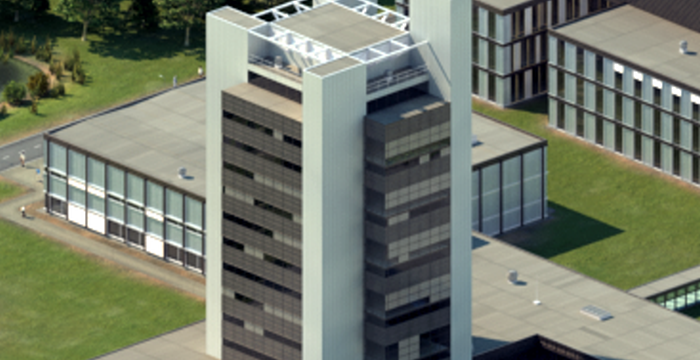
University of Twente
Horst Complex (building no. 20)
De Horst 2
7522 LW Enschede
Netherlands
University of Twente
Horst Complex
P.O. Box 217
7500 AE Enschede
Netherlands