I have lived, studied and worked in six countries (Syria, Austria, Italy, Germany, Poland and The Netherlands) :D
I am a PhD candidate at the University of Twente. My research focuses on the numerical and experimental process optimization of laser powder bed fusion technology (LPBF). I utilize existing numerical models/tools and develop new ones to predict materials processability for LPBF. In addition, I calibrate and validate the simulation results with experiments.
I completed my undergraduate studies in a five years BSc program in āMechanical Engineeringā at Damascus University. During this, I worked as a mechanical designer and completed a research internship at Vienna University of Technology; investigating crack formation during continuous casting. In 2012 I graduated with honours and obtained academic excel awards in 2010, 2011 and 2013. After that, I worked as a mechanical engineer for about two years.
I have always been interested in computational tools to solve engineering and physics problems. This motivated me to do a MSc degree in a related field. In 2014, I was awarded a full scholarship from the European Commission to complete my MSc studies in the joint MSc Erasmus Mundus degree program āMathModsā. In 2016, I graduated with a double major MSc degree in āMathematical Engineeringā and āComputational Materials Scienceā.
More about me: I like reading, hiking, astronomy, fitness activity, meeting friends and travelling.
Expertise
Material Science
- Three Dimensional Printing
- Powder
- Particle
- Laser Powder Bed Fusion
Engineering
- Additive Manufacturing
- Powder Layer
- Simulation
- Characteristics
Organisations
Project: Numerical and Experimental Studies of Processes Governing Selective Laser Sintering/Melting (Laser Powder Bed Fusion-Additive Manufacturing).
Selective Laser Sintering / Melting (SLS/SLM) is an additive manufacturing process consisting of various stages, each requiring different process parameters. Typically, the optimization of those parameters to achieve the desired final properties is done by performing costly experimental trials. I am developing a computational model that will help reduce the number of trials, thereby reducing the manufacturing costs. In addition, allowing processability predictions for new materials. This is achieved by comparing numerical results obtained through simulation of individual production steps against experimental data on the same processes (powder spreading process, powder sintering/melting and printed parts mechanical characterization), to advance the development of accurate predictive models.
Publications
2024
2023
2021
2020
Research profiles
Address
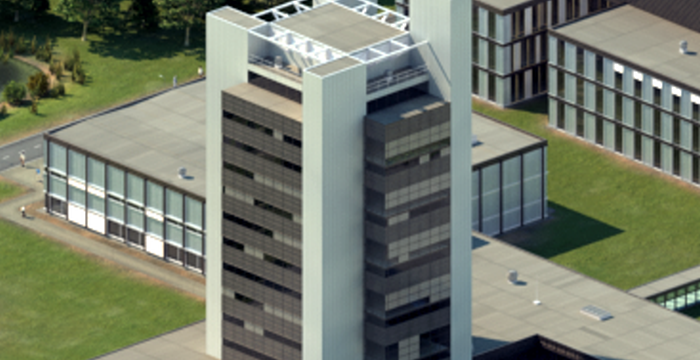
University of Twente
Horst Complex (building no. 20), room N256
De Horst 2
7522 LW Enschede
Netherlands
University of Twente
Horst Complex N256
P.O. Box 217
7500 AE Enschede
Netherlands