Dr. Tanmaya Mishra works as an Assistant Professor at the University of Twente with the Surface Technology and Tribology Lab. He was recently granted the DeepNL, NWO research grant for Tenure track call for his project "μFAULT - scaling friction from micro-contacts to faults at the reservoir scale" for research on friction in earthquakes.
His research background is in tribology with projects on multiscale friction and wear modelling, coatings, metal forming and earthquakes with efforts towards developing the research line on 'Geotribology'. In the field of 'geotribology', he aims to study and develop friction and wear models for tribological applications in geomaterials like rocks and soil. In the context of interfaces, he focusses on stick-slip (transitional) interfaces with applications in geophysics (earthquakes), ropes, lithography, drilling and geotechnics. He also enjoys teaching Bachelors' ME Tribology courses in University of Twente and Vrije Universiteit Amsterdam.
Prior to this he worked as a post doctoral researcher in the Experimental Rock Deformation Group at Utrecht University. He completed his PhD in December 2019 at the University of Twente, with his thesis on "Modelling of ploughing by an elliptical asperity through a zinc coated steel sheet - with application to modelling friction in deep-drawing."
He completed his Masters in Erasmus Mundus program on Tribology, TRIBOS across University of Leeds, University of Ljubljana and Lulea University of Technology in 2015. He started his career as a Mechanical Engineer working on heavy vehicles transmission for TATA Motors after graduating as a Mechanical Engineer from NIT Rourkela, India in 2011.
Expertise
Material Science
- Friction
- Sheet Metal Forming
- Material Point Method
- Steel Sheet
- Coating
Engineering
- Sheet Metal
- Metal Forming
- Models
Organisations
Dr. Tanmaya Mishra has worked on research projects in Tribology with applications in hydraulic machinery, metal forming and geophysics. Through this he has gained research interests in coatings, lubricants, non-linear mechanics, earthquake geomechanics, and skills in numerical tribology simulations and experiments.
Publications
2024
2021
2020
Research profiles
Courses academic year 2024/2025
Courses in the current academic year are added at the moment they are finalised in the Osiris system. Therefore it is possible that the list is not yet complete for the whole academic year.
Courses academic year 2023/2024
Current projects
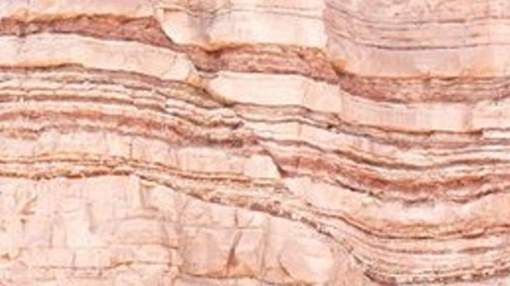
FASTSLIP: Bridging Dynamic Fault Slip Multiphysics to All Relevant Scales of Induced Seismicity
Earthquakes often result in damage to buildings and infrastructure and sometimes loss of human lives. Induced earthquakes due to human activities like gas extraction, are the result of fast slip on powder‐filled pre‐existing faults in the subsurface due to a rapid breakdown of their strength. The physical mechanisms contributing to the rapid failure remain unclear. In this project we will perform experiments at scales of a single rock grain to millions of grains combined with computer models to investigate these weakening mechanisms. Our results will help to better constrain the hazard of induced earthquakes.
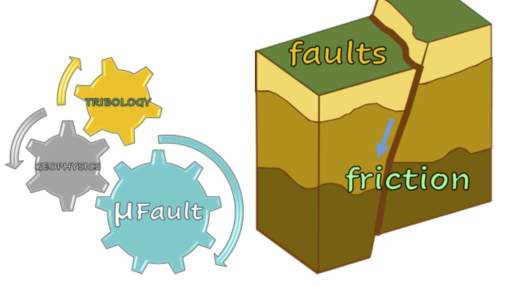
μFAULT - scaling friction from micro-contacts to faults at the reservoir scale
Fault friction: small scale, large consequences
Earthquakes reflect the phenomenon of sudden slip when the frictional strength of faults in the Earth’s crust is overcome. This project aims to understand the physical processes controlling this sudden failure through numerical modelling and lab experiments at the microscale and applying the results to obtain large-scale models for earthquakes caused by gas extraction, geothermal energy production and subsurface storage. Gaining deeper knowledge of frictional mechanisms in faults at different length scales will help improve forecasting of earthquakes and other subsurface phenomena, caused by increasing human intervention.
Finished projects
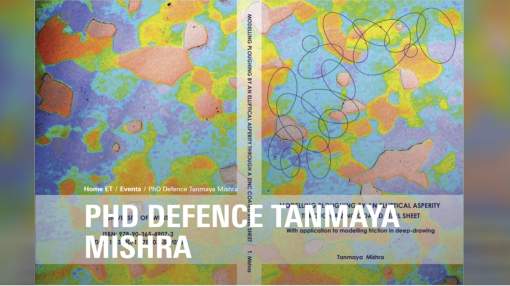
Model based surface texture design for zinc coated metal sheets
Modelling ploughing by an elliptical asperity through a zinc coated steel sheet: with application to modelling friction in deep-drawing
Modelling of friction in deep-drawing process is critical to the design to the product. Typically, the steel sheets used in deep-drawing are coated with a thin zinc layer by hot dip galvanization. The zinc coated steel sheets are further lubricated and provided with the required surface texture, amongst other things, to optimize the frictional stresses in a deep-drawing process. The friction in deep-drawing during loading and sliding of the tool against the sheet, in boundary lubrication regime, results from shearing of the interfacial layers, but also from ploughing of the flattened sheet surface by rigid tool asperities. The asperities on the surface of the tool have been mapped with elliptic bases of varying sizes and orientation relative to sliding direction. The current thesis aims to model the ploughing behaviour by an elliptical asperity sliding through a zinc coated steel sheet. The friction in ploughing results from the plastic deformation of the sheet substrate and the shearing of the interface between the asperity and the substrate. These two factors are also part of a material point method (MPM)-based numerical ploughing model and a simplistic analytical ploughing model. Both the numerical and the analytical models have been extended to calculate the friction in ploughing of uncoated and zinc coated steel sheets by elliptical and spherical asperities of varying sizes, ellipticity ratios and orientation relative to the sliding direction. The analytical ploughing model has been developed for rigid-plastic material behaviour of the substrate and a constant interfacial frictional shear strength. In contrast, experimentally characterized material strength models, yield functions and interfacial friction models have been implemented in the MPM-based ploughing model. An experimental characterization technique to measure the interfacial shear strength has been developed for unlubricated and lubricated, uncoated and zinc coated steel sheets at varying loads and sliding velocities using line contacts in linear sliding experiments. Also an experimental characterization technique to determine the yield criteria for the (anisotropic) temper rolled zinc coating on steel sheet has been developed using Knoop indentations. The method has also been applied on cold rolled steel sheet and validated using standard yield criteria. The experimentally characterized parameters for the interfacial friction model, the yield function and the yield criteria for the steel sheet and the zinc coating on steel sheet have been implemented in the MPM model to perform simulations of ploughing asperities with properties close to the reality. Further ploughing experiments are performed using indenters with spherical tips of varying sizes and indenters with ellipsoidal tips with varying size and orientation relative to sliding direction. Further, experiments have been performed with varying ploughing direction on unlubricated and lubricated steel sheets, lubricated zinc block and lubricated, temper rolled and unrolled zinc coated steel sheets under a range of applied loads. The developed MPM-based ploughing model is validated using experimental results such as the measured friction force and measured ploughing depth. The measured results are found to be in very good agreement with calculations. The MPM-based ploughing model results are also compared and shown to agree well with the analytical model results for simpler rigid-plastic material behaviour of the substrate. The developed MPM-based ploughing model and the analytical models can therefore be used as robust tools in computing friction in single asperity ploughing. The models can be utilized to accurately model friction due to ploughing for tool sheet contacts in a deep-drawing processes. In this way, the models describing friction in deep-drawing processes can be improved.
News on utwente.nl
FASTSLIP: BRIDGING DYNAMIC FAULT SLIP MULTIPHYSICS TO ALL RELEVANT SCALES OF INDUCED SEISMICITY
DRILL BUG: DEVELOPING BIO-INSPIRED DRILLING METHODS IN EXTREME ENVIRONMENTS
Address
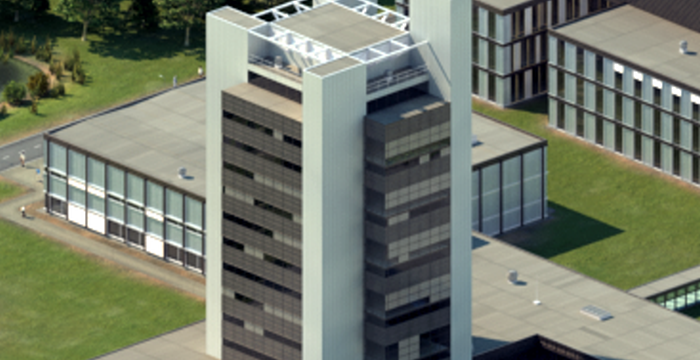
University of Twente
Horst Complex (building no. 20), room N104
De Horst 2
7522 LW Enschede
Netherlands
University of Twente
Horst Complex N104
P.O. Box 217
7500 AE Enschede
Netherlands